Unknown Facts About Alcast Company
Unknown Facts About Alcast Company
Blog Article
The 25-Second Trick For Alcast Company
Table of ContentsThe Best Guide To Alcast CompanyAbout Alcast CompanyThe 5-Minute Rule for Alcast CompanyWhat Does Alcast Company Mean?Everything about Alcast CompanyThe 30-Second Trick For Alcast Company
The refined distinction depends on the chemical material. Chemical Contrast of Cast Light weight aluminum Alloys Silicon advertises castability by minimizing the alloy's melting temperature and boosting fluidness during spreading. It plays a vital role in permitting complex molds to be filled up properly. Furthermore, silicon adds to the alloy's strength and use resistance, making it important in applications where durability is crucial, such as vehicle parts and engine elements.It likewise improves the machinability of the alloy, making it less complicated to process right into completed items. This way, iron adds to the overall workability of aluminum alloys. Copper raises electric conductivity, making it advantageous in electric applications. It likewise improves rust resistance and includes in the alloy's overall strength.
Manganese contributes to the strength of light weight aluminum alloys and boosts workability. Magnesium is a lightweight component that provides strength and impact resistance to aluminum alloys.
Fascination About Alcast Company
It enables the manufacturing of lightweight elements with excellent mechanical buildings. Zinc enhances the castability of light weight aluminum alloys and helps control the solidification process during casting. It improves the alloy's stamina and hardness. It is typically located in applications where detailed shapes and great details are essential, such as ornamental castings and specific automotive components.

The primary thermal conductivity, tensile stamina, return toughness, and elongation vary. Among the above alloys, A356 has the greatest thermal conductivity, and A380 and ADC12 have the lowest.
The Basic Principles Of Alcast Company
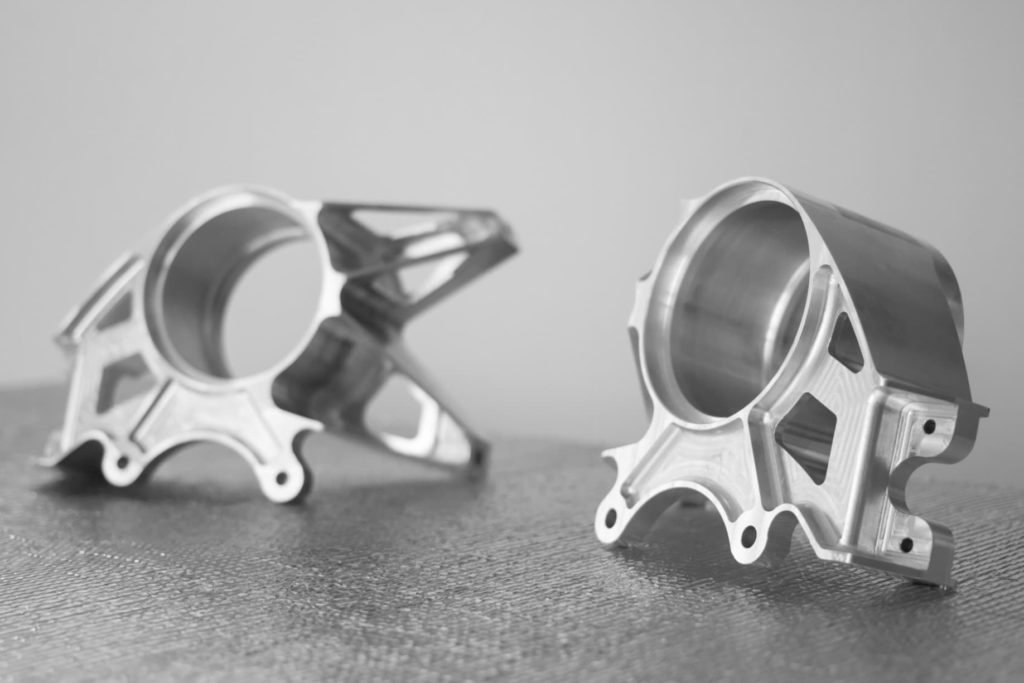
Its special homes make A360 a beneficial choice for precision casting in these markets, boosting product resilience and top quality. aluminum metal casting. Aluminum alloy 380, or A380, is a commonly utilized casting alloy with a number of distinct attributes.
In precision spreading, aluminum 413 radiates in the Consumer Electronics and Power Devices sectors. This alloy's premium deterioration resistance makes it a superb choice for outside applications, making sure lasting, sturdy items in the mentioned sectors.
The Best Strategy To Use For Alcast Company
The light weight aluminum alloy you pick will substantially affect both the casting process and the properties of the final product. Because of this, you should make your choice thoroughly and take an educated method.
Identifying one of the most appropriate light weight aluminum alloy for your application will certainly suggest considering a vast selection of characteristics. These relative alloy attributes follow the North American Die Casting Organization's guidelines, go and we have actually split them right into 2 classifications. The very first category addresses alloy characteristics that affect the manufacturing procedure. The 2nd covers characteristics affecting the buildings of the last product.
Getting My Alcast Company To Work
The alloy you choose for die spreading directly influences numerous aspects of the spreading process, like exactly how very easy the alloy is to collaborate with and if it is prone to casting flaws. Hot cracking, additionally referred to as solidification breaking, is a normal die casting issue for aluminum alloys that can lead to internal or surface-level splits or fractures.
Particular light weight aluminum alloys are much more vulnerable to warm fracturing than others, and your option needs to consider this. It can harm both the actors and the die, so you should look for alloys with high anti-soldering homes.
Deterioration resistance, which is already a remarkable characteristic of light weight aluminum, can vary significantly from alloy to alloy and is a crucial particular to take into consideration relying on the ecological conditions your product will certainly be revealed to (aluminum casting company). Put on resistance is another residential property generally sought in aluminum items and can separate some alloys
Report this page